Processes
The green tanning revolution
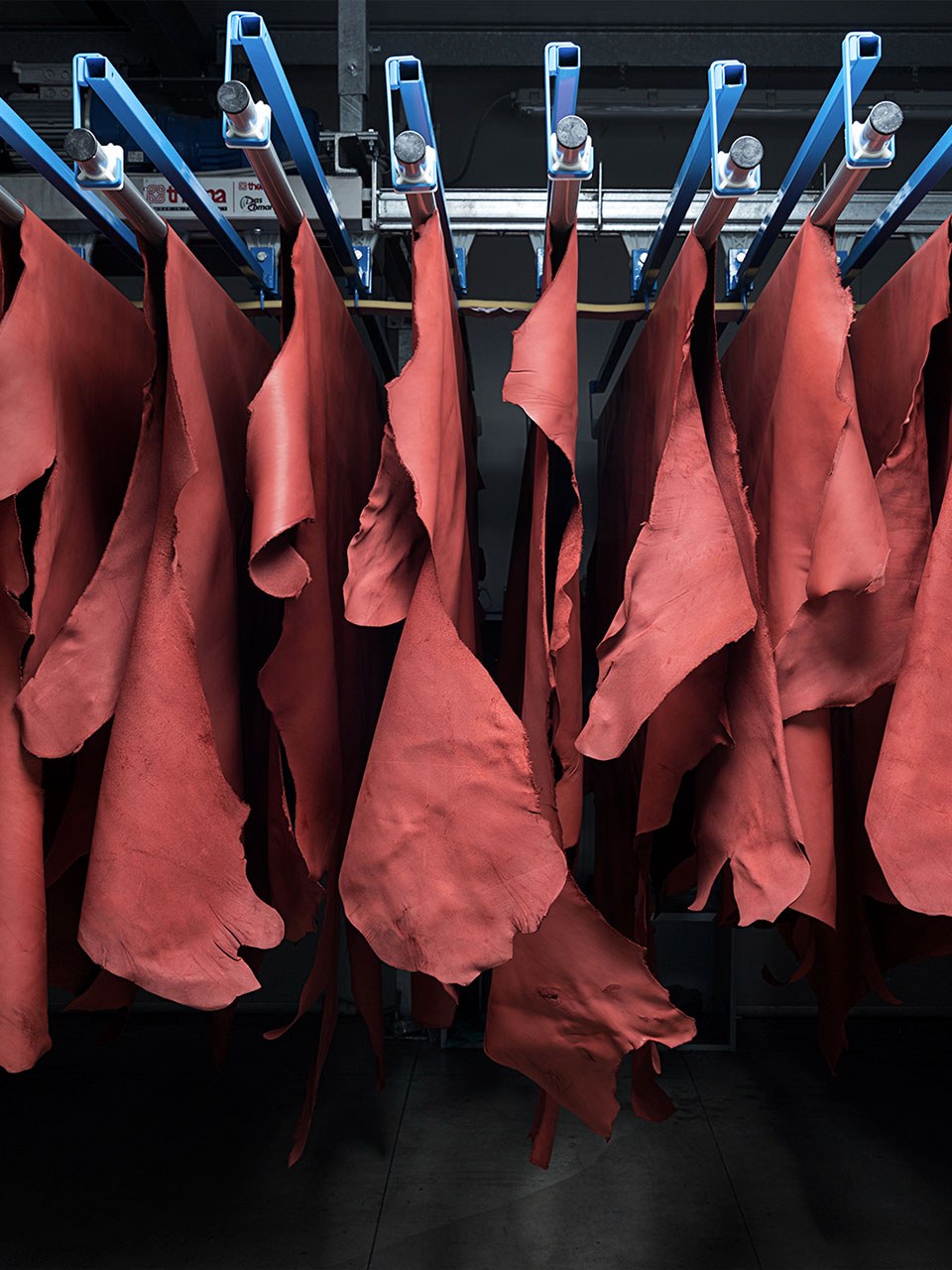
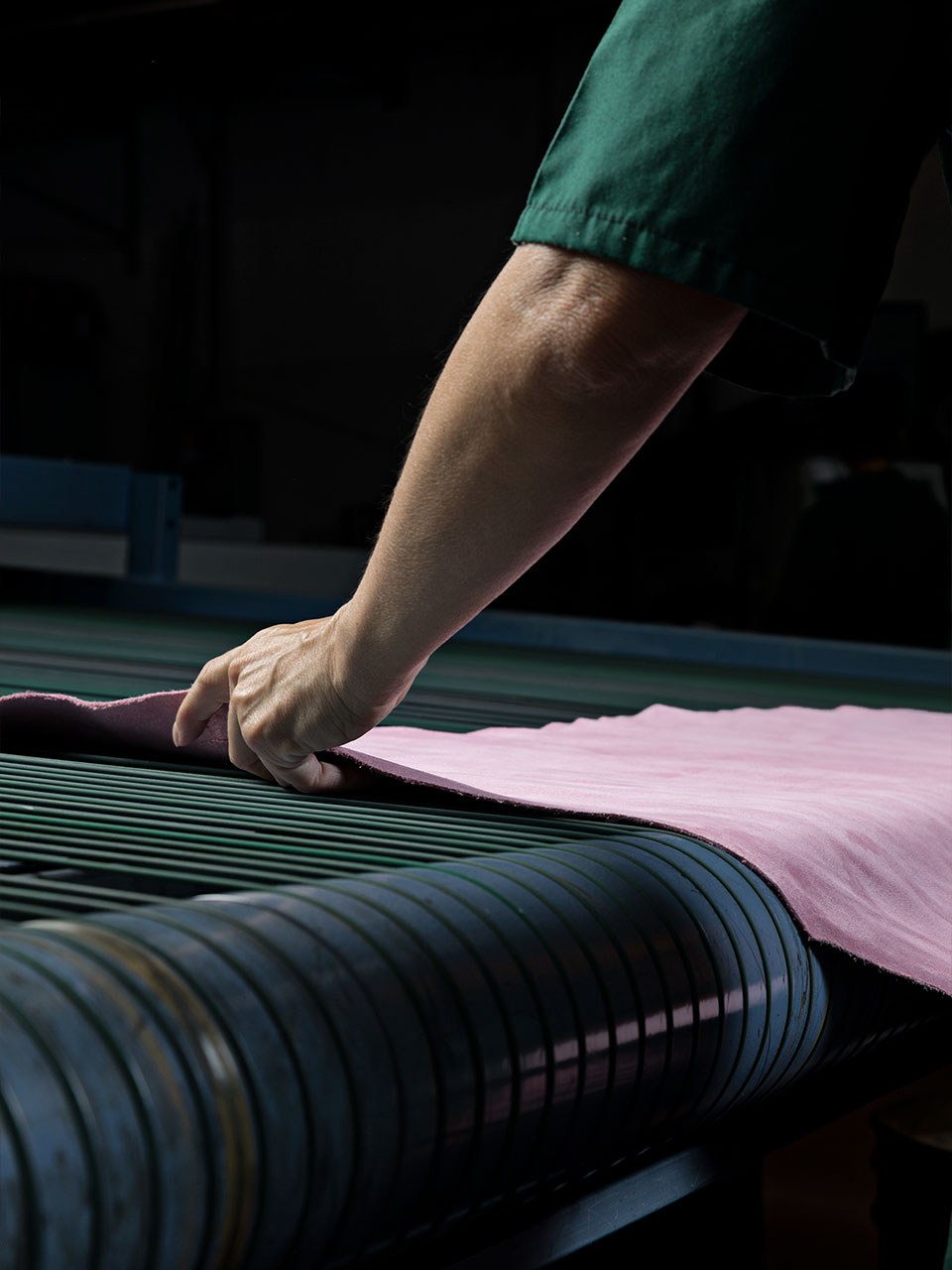
Intro
Towards a more sustainable production
As part of our ongoing commitment to sustainability and efficiency, Gruppo Mastrotto has dedicated significant resources to the innovation of its production processes.
This effort materializes in the adoption of advanced technologies and operational methodologies that enhance productive efficiency while simultaneously reducing the environmental impact of our activities.
Key areas of this innovation process include reducing the use of chemicals, saving water and valorizing production waste.
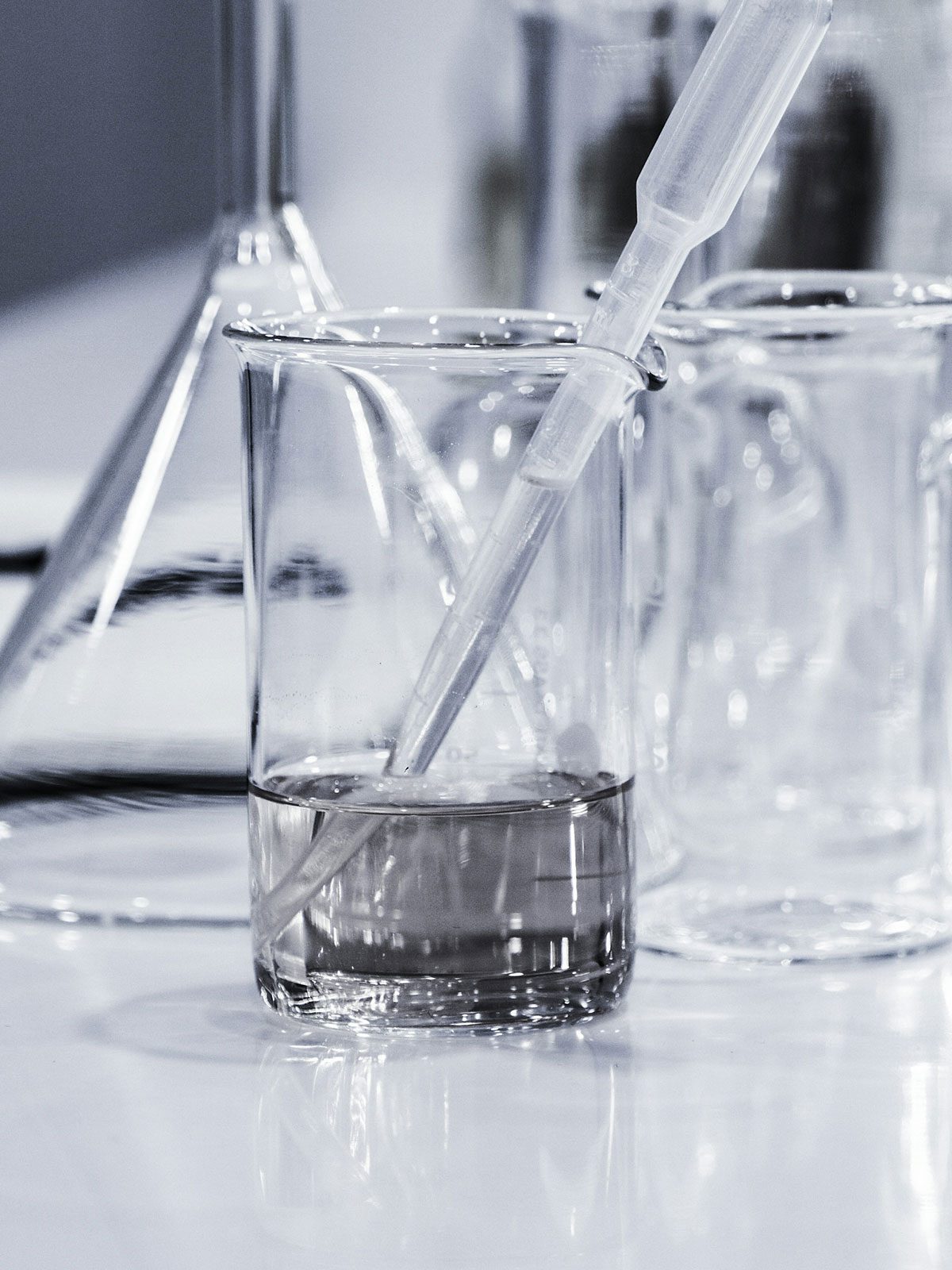
One of our most important process innovation efforts is to reduce the use of chemicals in our tanning and finishing cycles.
We have gradually introduced the use of plant-based tanning agents and selected more sustainable alternatives to traditional chemicals, while also improving the safety and quality of the working environment.
This approach has made it possible to maintain the high quality and distinctive characteristics of our leathers, while becoming kinder to the environment.
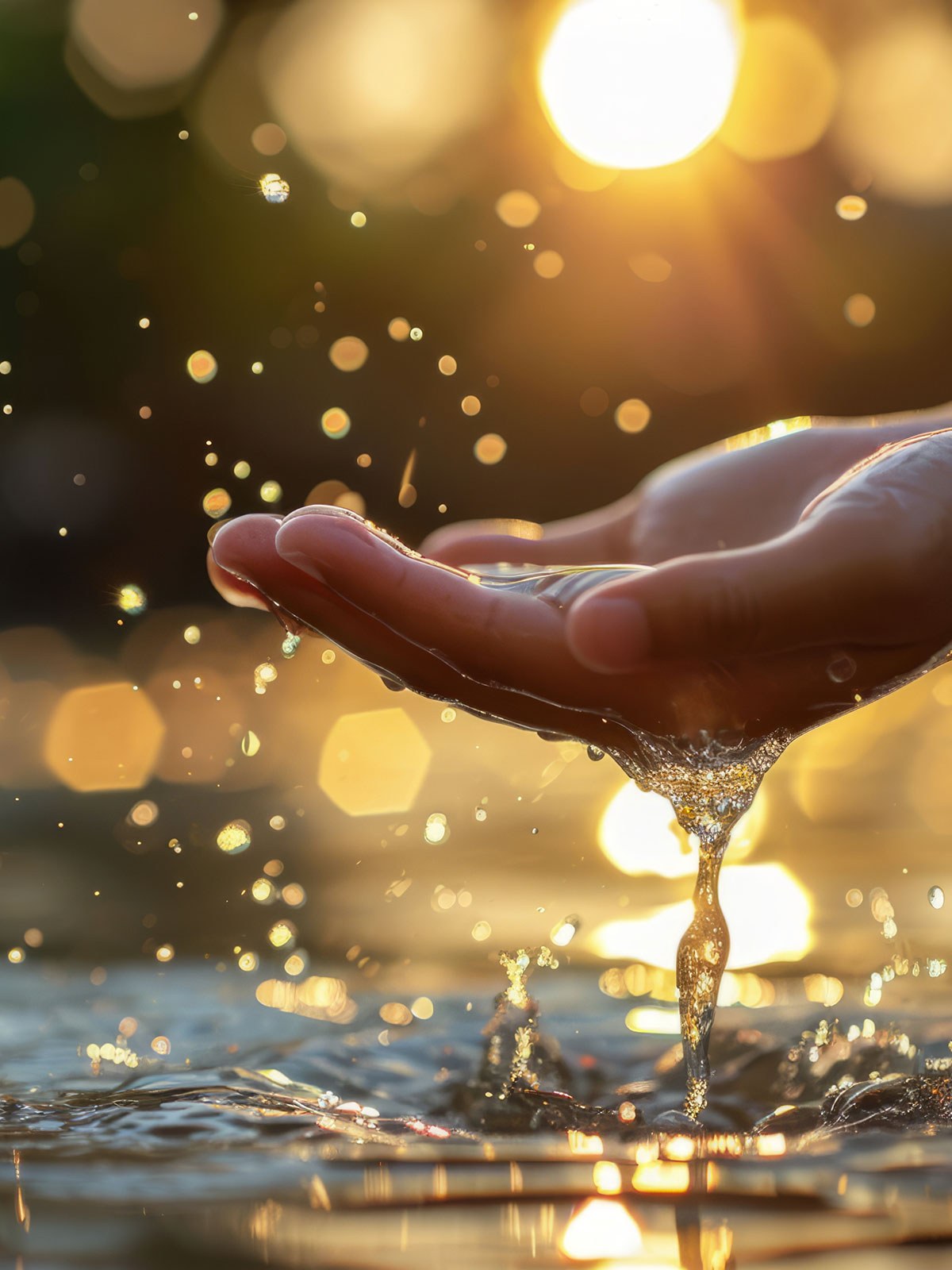
Saving water is another cornerstone of our process innovation strategy. Since leather production is traditionally water-intensive, we have adopted technologies significantly reducing its consumption.
These technologies include advanced recycling and purification systems that allow to reuse a considerable amount of the water used in our production processes.
This practice reduces the volumes drawn from natural sources and the wastewater treatment load, helping to preserve local resources.
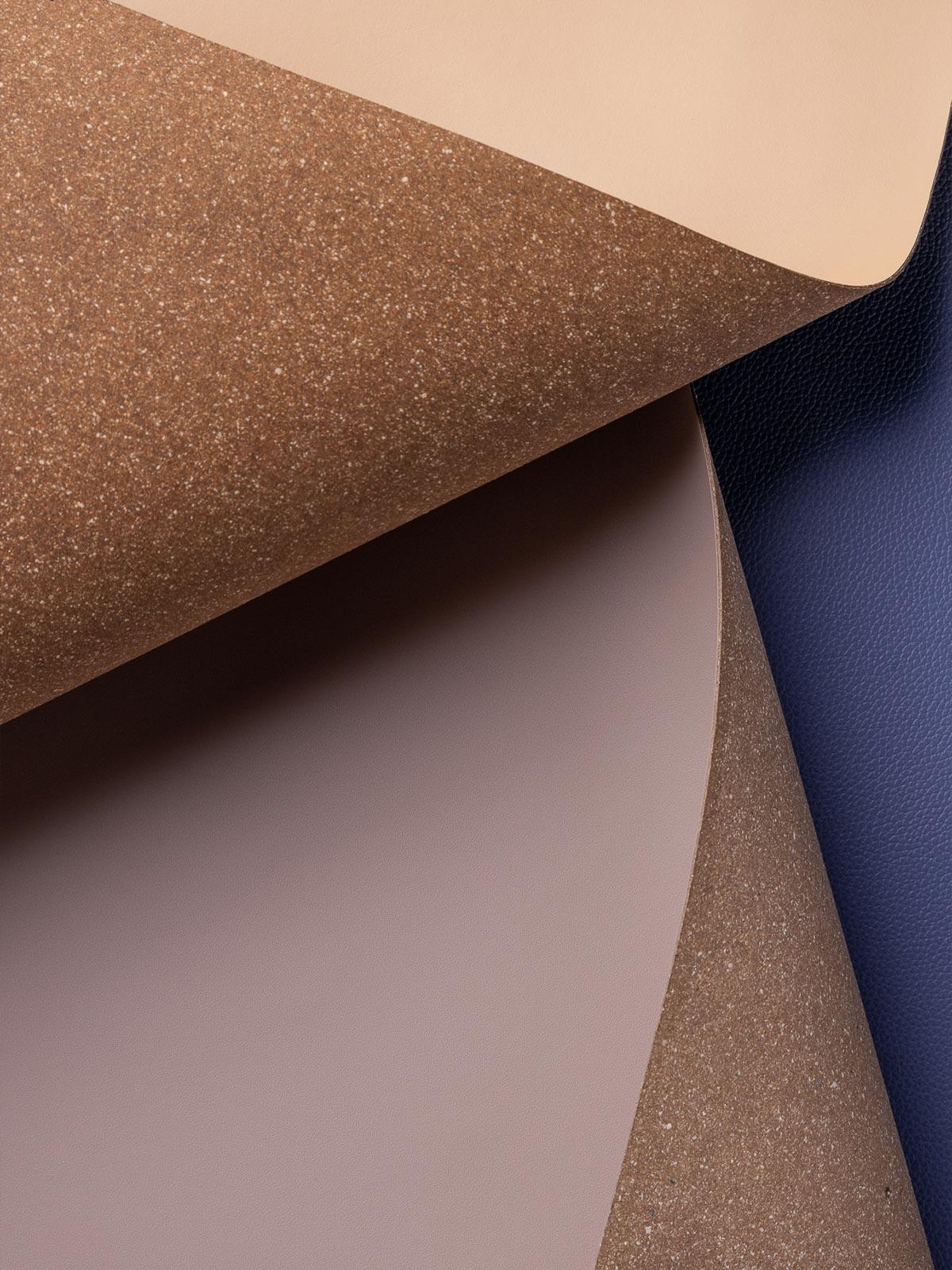
The last aspect of our process innovation is the optimisation of production waste.
Gruppo Mastrotto is committed to minimising waste by recovering processing cycle waste, reusing residues and by-products or transforming them into new materials, to create a process that tends as much as possible towards zero-waste.
Today, more than 93% (over 20% higher than the industry average) of the waste generated from our tanning processes is transformed and reused in other sectors, from biostimulants and fertilisers for agriculture to collagen for cosmetics and gelatine for the food industry.